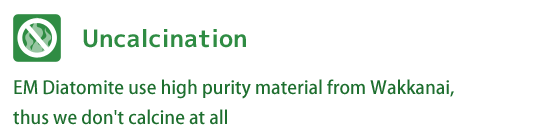
Almost manufactures do calcine the rock of diatomite.
This is because they want to remove impurities and stabilize the product.
However, it will cause another problem.
The main constituent of diatomite is SiO2 (silicon dioxide). When it is heated with high temperature, it will be glass. As you know, glass doesn't work as humidity control. To calcine diatomite invites covering pores which is feature of it. Many manufactures do it with from 800℃ to 1200℃ temperature, but as you can understand from below graph, the effect of humidity control will be down gradually when the temperature is over 800℃ and gone at 1100℃.
This is because they want to remove impurities and stabilize the product.
However, it will cause another problem.
The main constituent of diatomite is SiO2 (silicon dioxide). When it is heated with high temperature, it will be glass. As you know, glass doesn't work as humidity control. To calcine diatomite invites covering pores which is feature of it. Many manufactures do it with from 800℃ to 1200℃ temperature, but as you can understand from below graph, the effect of humidity control will be down gradually when the temperature is over 800℃ and gone at 1100℃.
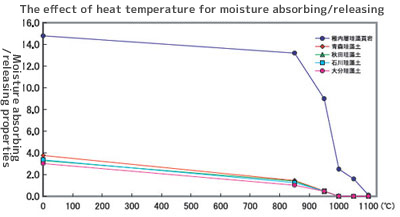
Besides, needle-shaped glass matter, cristobalite is created during the process of calcination and it has been suspected of being carcinogenic. So a part of Europe and America prohibit using diatomite as plastering materials.
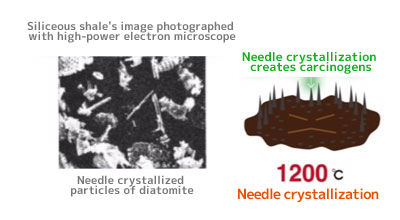
As for carcinogenic, it is still under studying though, it is the best to use uncalcined product.
EM Diatomite is safe "uncalcined" one. The amount of moisture control of Wakkanai siliceous shale is three times as much as others.
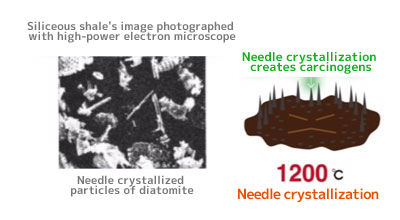
As for carcinogenic, it is still under studying though, it is the best to use uncalcined product.
EM Diatomite is safe "uncalcined" one. The amount of moisture control of Wakkanai siliceous shale is three times as much as others.
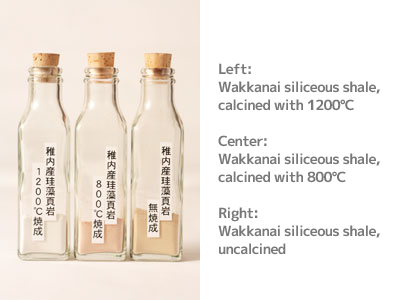